An Unbiased View of Manufacturing Industriess
Wiki Article
The 10-Minute Rule for Additive Manufacturing
Table of ContentsIndicators on Additive Manufacturing You Should KnowNot known Details About Plastic Manufacturing The Basic Principles Of Hon Hai Precision The Only Guide to Lean ProductionExamine This Report about Manufacturing IndustriesThe 2-Minute Rule for Hon Hai Precision
The text on this page is an example from our full White Paper 'Injection Moulding for Purchasers' - * Example text * - for full guide click the download switch over! Intro This guide is intended for individuals that are looking to resource plastic mouldings. It provides a much needed insight into all that is entailed with developing plastic components, from the mould tool required to the moulding procedure itself.If you intend to check out further, the overview covers kinds of mould tools, in addition to special completing procedures such as colours & plating. Words that are underlined can be discovered in the glossary in the appendix ... Component I: Moulding: The Essentials The Benefits of Injection Moulding Plastic shot moulding is a really precise process that offers several benefits over other plastic processing techniques.
Accuracy is ideal for very intricate parts. You can hold this moulding in the hand of your hand as well as it has employers, ribs, steel inserts, side cores and also holes, made with a moving shut off function in the mould device.
Everything about Additive Manufacturing
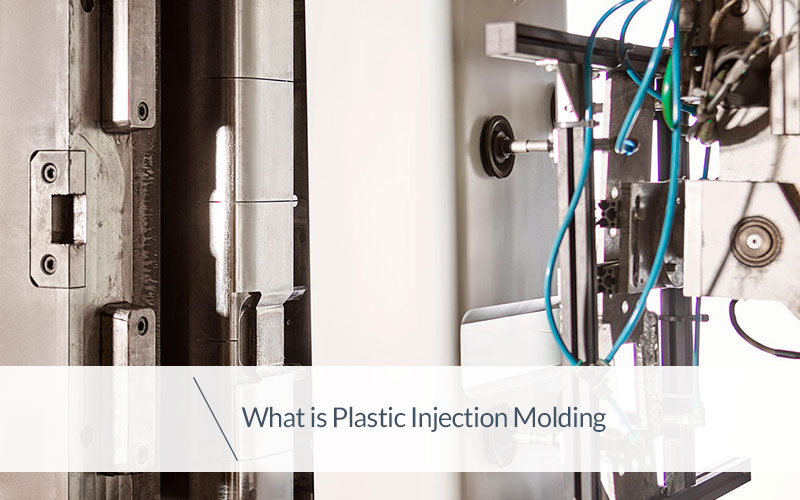

Manufacturing Things To Know Before You Get This
from material feed & melting; material injectionProduct cooling time cooling down ejection and also the re-closing of the mould tool ready for all set next cycle. Draft angles - The wall surfaces of a moulded component need to be slightly tapered in the instructions in which the component is ejected from the mould device, to enable the part to be ejected conveniently.Ejector stroke - The pushing out of ejector pins to expel the moulded part from the mould device. Ejector stroke speed, length as well as timing requires to be very carefully regulated to avoid damage to the ejectors as well as mould device, yet at the very same time make the moulding cycle as short as feasible.

The Basic Principles Of Die Casting
Ribs - When a plastic part has thin walls, ribs are contributed to the layout to make the slim walls more powerful Side cores - Side activity which produces a feature on a moulded part, at an opposing angle to the typical opening direction of the mould device. plastic manufacturing. The side core needs to be able to withdraw as the plastic component can not be ejected otherwise.
Wall surfaces - The sides of a moulded part The text on this page is a sample from our complete White Paper 'Injection Moulding for Purchasers'.
Shot moulding is commonly utilized for manufacturing a selection of components, from the tiniest parts to entire body panels of vehicles. Shot moulding uses a special-purpose machine that has three parts: the shot device, the mould and also the clamp.
Little Known Questions About Oem.
Process characteristics [edit] Injection moulding utilizes a ram or screw-type bettor to require molten plastic or rubber product right into a mould cavity; this solidifies into a form that has adjusted to the shape of the mould. It is most commonly utilized to process both thermoplastic and also thermosetting polymers, with the quantity used of the former being considerably higher.: 13 Thermoplastics are common as a result of features that make them extremely suitable for injection moulding, such as simplicity of recycling, convenience for a vast range of applications,: 89 and capacity to soften and also move on heating.In multiple tooth cavity moulds, each dental caries can be identical as well as create the continuous production exact same components or can be unique and create numerous various geometries throughout a single cycle.
The screw provides the raw material onward, blends and homogenises the thermal and viscous distributions of the polymer, and also lowers the required home heating time by mechanically shearing the material and adding a considerable amount of frictional home heating to the polymer. The product feeds onward via a check shutoff and also accumulates at the front of the screw into a quantity called a shot. When sufficient material has gathered, the product is forced at high stress and speed into the component developing tooth cavity. The precise amount of shrinkage is a function of the resin being used, and also can be relatively foreseeable. To protect against spikes in stress, the procedure generally makes use of a transfer setting corresponding to a 9598% complete cavity where the screw shifts from a consistent speed to a continuous pressure control.
The Facts About Manufacturing Uncovered
As soon as the screw reaches the transfer setting the packaging pressure is applied, which finishes mould dental filling and also makes up for thermal shrinkage, which is rather high for thermoplastics family member to several other products. The packing stress is used up until eviction (tooth cavity entryway) strengthens. Due to its small important site size, eviction is generally the starting point to solidify with its whole thickness.: 16 Once eviction solidifies, no even more material can get in the cavity; accordingly, the screw reciprocates as well as gets product for the following cycle while the product within the mould cools down so that it can be expelled and be dimensionally secure.Report this wiki page